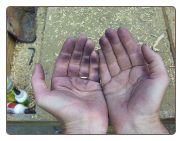 Red Oak has a lot of tannin in it (once used as a dye) and it still works.
|
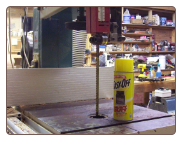 A light coating of Pam lubricates the blade and keeps it from gumming up. Easy Off will also take off the gum that seems to only collect on one side of the blade.
|
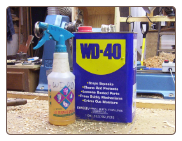 Buy it by the gallon, you'll need it.
|
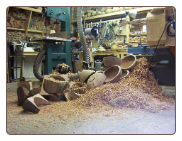 A days work
|
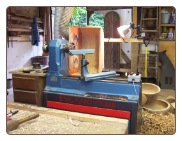 Vicmarc VL300 and dust collection hood
|
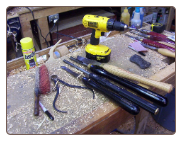 Basic tools, skew, Glaser 1/2" shallow, 3/4" bowl, 1" oval scraper
|
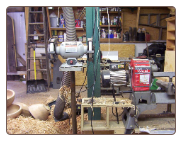 Grinder, I like it high and only a few steps away from the lathe, old lathe (only a year old but now obsolete) to right.
|
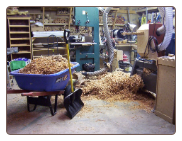 A snow shovel comes in handy even in the summer
|
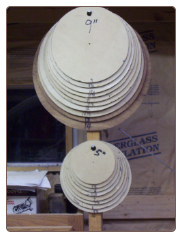 Precut layout discs made from scraps
|
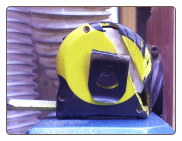 Finding tape measure in the saw dust, with the aid of my chain saw (it still works!).
|
 BEST USE OF A STANDARD SHEET OF SANDPAPER
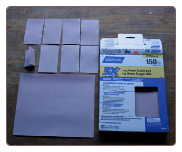 I find this is the best use of a sheet of sandpaper. Less waist and very handy.
|
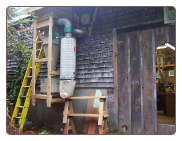 Dust collector mounted on the outside wall is less noisy and frees up more shop space
|
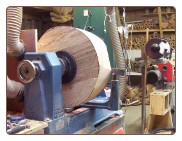 21" Ash blank mounted with screw chuck.
|
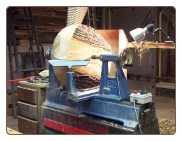 With large blanks like this I'll back it up with the tail stock. The tail stock adds aditonal support allowing for higher turning speeds and a more aggresive cut to remove more wood quickly.
|
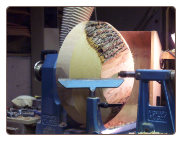 Start with taking off the corner first so that the blank will be more balanced and the speed can be increased for faster cutting.
|
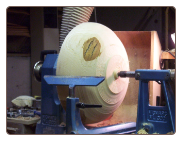 Just a few more passes and I'll be down to solid wood and refine the shape to it's final form.
|
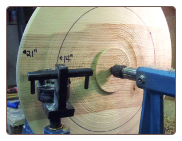 I've marked a 14" diameter line as a referance because my largest blade will only hollow out a 14" bowl. I've also left a tenon in the center to reverse mount the cored out center in the chuck.
|
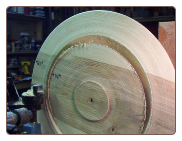 If it's done right, the core should only be hanging on by a small bit of wood at the center. A good pop with the heel of your palm should seperate the the inner core form the outer bowl. I also have a rubber dead blow mallet for when I've overreached the cutting capacity of my blade.
|
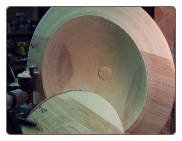 Here you can see the small nubbin left holding the core at the center bottom of the bowl.
|
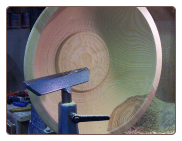 I follow-up by finish hollowing the bowl to a uniform thickness top-to-bottom and leave a boss in the bottom for reverse chucking. I don't use a formula or measure wall thickness for rough turned bowls. A uniform thickness thoughout the bowl wall reduces cracks and splits and warpage tends to be more uniform. Having the heartwood centered also leads to a more uniform and symmetrical warp to the bowl.
|
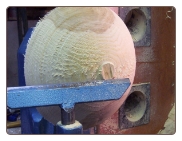 Here the core is revers-chucked and ready to have a foot cut into the bottom.
|
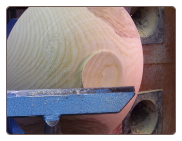 The foot should be approximatly 30% to 35% of the bowls diameter for utility bowls but this is also determined by the size of the jaws you happen to have. I have four chucks and keep diffrent size jaws on each (stopping to change jaws in annoying). Over time and many bowls turned you can guesstimate fairly accurately the diameter need to fit the jaws by eye. I'll do one quick check for proper size with a pair of calipers before I make the final cut.
|
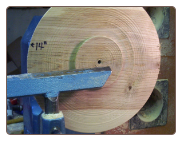 At this point you could core out another bowl and the tenon cut earlier would be put into service again for rechucking and cutting the foot. The hole drilled for screw chucking now makes initial hollowing a bit easier.
|
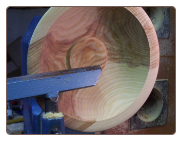 Again, I've left a boss in the bottom of the bowl for revarse chucking and you can see in this picture that the heartwood is fairly well in the center of the bowl. I date and write the wood type on all my bowls in black sharpie. I add the wood type because after months or even years of collecting shop dust woods typs can be hard to distinqish one from another.
|
 SMALL BOWL BLANK CUTTING
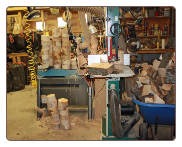 My stack of cut-offs (wrapped in plastic and ignored for a few months) yielded over 50 five and six inch maple and cherry bowls.
|
 RED OAK LOGS
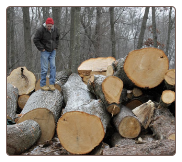 Red Oak logs
|
 Loading-up Black Oak
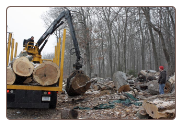 The only reason I know these logs are Black Oak is because they had a nice little identification plaque still nailed to the log.
|
 Unloading Copper Beech
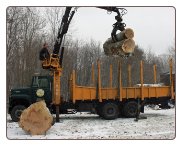 Unloading the Copper Beech. Each one of these logs weighed-in at about 4,000 lbs. (If you're wondering, the grapple has a weight gauge)
|
 A BIGGER SAW!
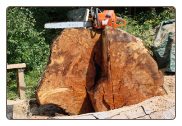 Husky 390XP, not the biggist they make but big enuph. The saw will take up-to a 36" bar but, I outfitted with a 28".
|
 Cutting Black Oak
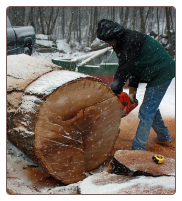 It didn't stop snowing for two days and we ended up with about 16" I'll wait for spring!
|
 Using painters plastic to slow drying.
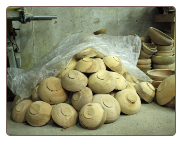 Thin painters plastic is good for slowing the drying processes. You will be able to see the condensation forming on the underside. Flip the plastic once a day until condensation stops forming and then let the bowls dry uncovered.
|
 ROUGH TURNED BOWL DRYING
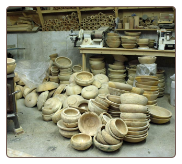 After a few months you can stack your roughs right-side-up to save some floor space.
|
 Search by Keyword
|
Note to readers: This page is a work in progress and I hope you come back again to see how it’s coming along. If you are looking for indepth professional instruction I highly recommend all of Richard Raffan’s books and CDs.
Note: All tool manufacturers safety guidelines should be adhered to and followed as appropriate for you own personal protection. My own disregard for personal safety should not be an example for you to follow.
 |
|
 |
|
 ABOUT TOOLS:
I love the look, feel, and usefulness of high quality tools. I've bought cheap tools when I couldn't afford any better and struggled with the shortcomings. When I can afford to buy the best (not always the most expensive) I do my homework before I buy. The following tools have served me well and should be given serious consideration.
Glaser Hitec 15V 1/2" shallow gouge: I've rough turned over one thousand bowls with this gouge and it still has quite a few more to go. The weighted handle design dampens vibration and gives added leverage. Keeps a sharp edge longer and touches-up quickly on the sharpening wheel. Can't beat it for large heavy out of round blanks. www.glaserhitec.com
Husqvarna Chain Saws: I have both the 359 and the 390XP. Great saws that start easy (low compression button) and run well even in the cold Northeast winter. www.husqvarna.com
Timberwolf Blades/Suffolk Machinery: Best band saw blades for cutting large green bowl blanks. Order direct and they cut any size to order. Check their website for everything you ever wanted to know about band saw blades. www.suffolkmachinery.com
Vicmarc Lathes and Chucks: The VL300 short bed bowl lathe is sturdy (cast iron), powerful (2hp/2.2kw motor) and simple. www.vicmarc.com
|
|
 |
|
 |
 Measuring the diameter
This Red Oak log was felled in March of 2008 and about half the log was cut and rough turned into blanks at that time. This bottom half I left sitting up off the ground on a couple of small rounds to keep it from rotting. Red Oak will catch a fungus almost instantly if left on the ground (spalted is a nice look but you will have to cultivate it for a year or so and there is no guarantee on your results).
 Length equal to diameter
The length of my cut is approximately the same as the diameter of the log, give-or-take an inch or so. Trees are seldom perfectly symmetrical and you can shorten or extend the length of cut to get the most out of the log.
 Cutting
The chain saw is the Husqvarna 357XP see www.husqvarna.com for a local dealer. This is my third saw (craftsman and smaller Husqvarna) and I highly recommend it. The best selling point is the Decompression button for easy starting.
 laying out bowl
Logs are somewhat symmetrical but seldom ideally so. I use a straight edge to find the best orientation for cutting the log in half. Ideally the pith will be an equal distance from both edges of the log. Often you will be presented with choosing between one very nice bowl orientation and one slightly less pleasing. Good bowl orientation choices made at the start will result in a rough turned bowl that warps evenly during the drying process and shows a predictable grain pattern when finished. Obviously, for creative reasons you can orient the bowl many different ways but you run the risk of creating more rough turned firewood that is warped and cracked beyond saving (I have several such pieces of artistic firewood).
 Bowl layout, bowl bottom cuts
Deciding on how much to cut off the sides for the bottom of the bowls is again somewhat dictated by how you have decided to orient your center cut. I look to remove all the bark, most if not all of the sap wood and a portion of heart wood. With Red Oak I only cut out the pith if the cracks extend out from the center more than an inch or two. I expect to turn away anything less on the lathe. The proportion of the foot in relation to the bowl width and height is one factor to consider and the other is how much sapwood you would like to leave on the outside of the bowl as a decorative feature. Bark and sap wood might be decoratively pleasing but are weak structurally and will not give the structural support on the bottom of the bowl needed for rechucking the bowl by its foot (I speak from experience on this account)*.
*Experience usually involves the violent release of stored kinetic energy resulting in minor to mildly severe bodily injury. While this kind of learning makes a lasting impression and can be surprising, exciting, and terrifying all in the span of a brief moment, it’s best avoided if at all possible.
 cutting sides of log first
I try to make my side cuts (bowl bottoms) parallel to the orientation of the center line (bowl top) of the log and I’m shooting for an even bowl thickness from side to side. Accurate cutting now will allow the bowl to sit flat and square on the band saw.
 Center cut, top of bowl
As with the side/bottom cuts, the center/top cut should be straight and parallel to the side/bottom cuts as much as possible. Being accurate now saves time later at the band saw and lathe.
 Bowl layout with precut pattern
An afternoon spent cutting bowl templates is well worth the time and effort. One 4X8 sheet of chip board should be adequate or you could use up old leftover scrap pieces that you couldn’t bring yourself to burn, as I did. An awl marks the center and I use a sharpie for the outline.
 Cutting out blank on the band saw
I started out with a 14” Delta band saw, but became so frustrated with its lack of power and cutting capacity (only 6” and ¾ hp) that I bought a bigger saw as soon as I could afford it. The Grizzly G514X saw (www.grizzly.com ) with a 12” depth of cut and at 2hp is fantastic. On sale this was a great bargain at about $900 which included shipping w/lift gate. It has all the bells and whistles the more expensive saws have, at a better price and Fine Woodworking Magazine gave it a best buy pick. I received my saw with shipping damaged doors and Grizzly customer service shipped out new doors within the week, no hassles, they were great.
 Completing the cut
Timber Wolf Band Saw Blades www.suffolkmachinery.com are the best for cutting green wood. I’m running their ½” X 3AS .032” blades. Suffolk sells blades direct and they're cheaper than the retail stores and you have access to their entire line of blades. Suffolk also has a great on-line tutorial on everything you ever wanted to know and more about band saw blades and their proper use. Using Pam to lubricate the blade is recommended and I’ve found it does improve ease of cutting and blade life. Their blades will cut through a 8” thick block of wood with ease. Timber Wolf blades are a bit pricy at about $27.00 each but I think it’s well worth the money.
 Bowl blank and firewood
Working from whole logs gives me the advantage of using the byproducts for firewood and mulch. The cost of the wood is a write-off at the end of the year and you save money on heating costs (life is good)
 Halfway there
A nice stack of bowl blanks gives me a sense of accomplishment after a mornings work. I’ll feel even better when I’ve finished roughing these blanks out and I can add them to my bowl bank (rough turned bowls are like money in the bank for a production turner). Also be aware that Red Oak tannin will oxidize bare steel almost instantly upone contact, clean off dust and shavings right away and apply WD40.
 Drilling for screw chuck mounting
A good quality cordless drill (½” 18V) is a must have and it's one of the most useful tools I’ve ever bought. On sale you can get a quality drill for about $150.00 and it's worth every penny.
 Screw chuck setup
Every lathe comes with a face plate but I’m not sure why, I’ve never used one and don’t plan on ever using one. Maybe I could use it as a paper weight to keep my sandpaper from curling due to summer humidity? When I bought my fist lathe, a Nova 1624/44 (www.teknatool.com ), I also bought a SuperNova2 Chuck to go along with the lathe as a matter of course. The advantages of using a chuck over a face plate are abundantly clear once you have seen it in action. Richard Raffan expertly demonstrates the versatility of a scroll chuck in his books and CDs. The SuperNova2 has served me well (I have two) and at $149.00 on sale it’s a good buy. You will also have to shell out another $25.00 for the insert to match your lathe. The jaws that come with the chuck are fine to get you started but you really need to buy 100mm and 130mm jaws to add more versatility. I just bought a Vicmarc VM120 chuck (www.vicmarc.com ) with step jaws. Vicmarc is the gold standard in lathes and chucks but the price reflects the high quality. Woodturners Catalog (www.woodturnerscatalog.com ) currently offers the best price at $269.99 w/insert.
 Mounting blank on chuck
The worm-wood screw that comes with the chuck has been adequate for almost everything. I’ve put on it so far, even up to 16”W X 6”H Red Oak blanks. On something this big I started out also backing it up with the tail stock for the outside rough turning but now I don't even bother. I've recently turned 22"w x 8"h ash without the tailstock.
 Rough turning outside of bowl
Rough turning the outside of the bowl consists mostly of removing all the bark and most if not all of the sap wood. Leaving sapwood can add an attractive contrast to the outside of your bowl but you run the risk of this wood cracking and splitting because sapwood dries much quicker than heartwood. When rough turning bowl blanks, your final bowl shape design decisions need to be made at this time. If you leave your wall thickness a bit on the fat side you will leave yourself a bit more latitude on your final shape and any embellishments you might like to add. Leaving as little as 1/4 inch extra wall thickness now can yield a wide range of design options later on when you finish turning the bowl. The trade off is you run the risk of having a higher percentage of split bowls down the line as they dry.
 Truing up the face
On the face I only cut in towards the center about half way. If my blank wasn’t cut right down the center of the log, I’ll turn away wood until the pith is removed and then a bit more. Turning away the pith can also be done when the bowl is re-chucked for hollowing.
 Turned foot for remounting in the chuck
I like to turn the foot just shy of the max diameter of the jaws but not so wide that the foot won’t fit into the jaws after the foot warps a bit oval during drying. Adjusting a set of calipers to this width takes the guess work out of the process. I’ve also made my own fixed caliper out of shop scraps (see sidebar) to save the cost of having a half dozen calipers dedicated to one measurement.
 Hollowing out inside of the bowl
Using a McNaughton system to core out two or three additional bowls from one blank is ideal but that’s a process best learned from a master turner. Mike Mahoney is the best authority on coring out bowls and Richard Raffan also gives a good account of how it’s done. The $285 you’ll need to spend is worth it but, you can live without it when you are just starting out. Drilling a center hole to gauge how deep you want to hollow is a good idea and it makes getting started a bit easier. Always cut from larger to smaller as you hollow the bowl. As the bowl dries the rim will distort more than the base. Leaving the rim thicker than the base will give you the necessary wall thickness to preserve the depth of the bowl you originally planned on. If you find the bowl has warped beyond your available rim thickness all is not lost, you just cut the rim down until you have enough wall thickness to work with. A wall thickness 10% of the bowl width is the rule of thumb.
 almost done
It doesn’t hurt to knock off the sharp edges on the inside and outside of the rim and I’ve heard it helps prevent the rim from splitting. I also turn a rabbit in the bottom of the bowl for reverse chucking. Again, I eyeball how wide to cut the rabbit in the pursuit of my motto, “less time measuring is more time for turning”, and if I’ve made a good guess I can remind myself of how wonderful I am (self congratulation is balanced by the dejection that comes after you turn through the bottom of a bowl or when the bowl explodes in your face as your finishing off the rim).
 Basic salad bowl
Drying bowls is a process of Natural Selection. It’s like the mother turtle laying her eggs on the beach. She lays hundreds of eggs and then just swims away not knowing or caring how many of her babies will grow to adulthood. Roughed out bowls must be like those eggs to the turner. Pile them up in a corner and just turn your back on them not knowing or caring if they will ever become finished bowls. Like the baby turtles who will get devoured only moments after they hatch or later as they struggle to reach the water, some bowls will split and crack beyond salvaging. Not many will be lost, but it’s foolish to get attached to your rough bowls because they may ultimately be lost to the whims of chance or a moment of lost concentration. This is a good thing because bowls that split in the drying process, of their own accord, are best used as firewood. Bowls that come through the ordeal of having their guts carved out and left to dry can be expected to endure the ensuing torture of finish turning and the ultimate test of daily use. I must admit to becoming attached to a few bowls when they came off the lathe and to anticipating the final turning knowing that I may be disappointed in the end.
 Date and set aside to dry
I date the rim with a black sharpie; month, day, year and the wood type. If you only have a few roughs wood type is not crittical but, if you have several hundred at any given time it will help you keep track of what you have (after sitting and collecting dust for a year or two they tend to all look the same). I then stack the bowls on the floor under a bench for a few weeks or months where it’s cooler and damper. In the humid summer months it’s good to give the roughs a few extra months to stabilize. In the dry winter months as little as a month may be adequate. If the wood is very wet I'll drape the pile of bowls with a sheet of clear plastic and flip the plastic over every day until the condensation no longer collects on the underside.
|
 4' DIAMETER COPPER BEECH LOG BUTT. Tree was cut 2-9-2010
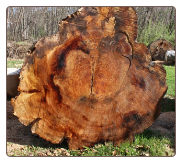 I hosed the end down to highlight the color. If you find a big log intimidating, just get a bigger saw! April 14, 2010
|
 SCRIBE A LINE FOR THE CROSS CUT
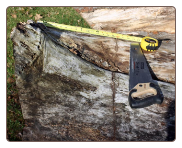 I'm cutting for 12" to 13" bowls but adding a couple of inches to give myself a little room for end grain checking.
|
 SIDE CUTS
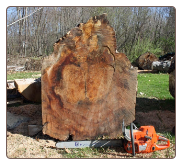 Cutting the slight flair off the sides will allow the log to sit flat and stable when I roll it over. (no shimming needed). Husky 390xp with 28" bar.
|
 CUT AND SEPARATE THE SLICE
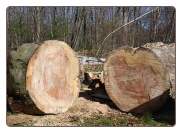 A small sheet of plywood under the flat side will help keep the saw out of the dirt.
|
 BOWL BLANK CUT PLAN
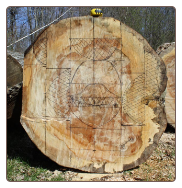 You need not go to the trouble of marking out every cut. I'll just mark the major vertical cuts and decide the rest later. I do take the time to find and mark any knots or problematic defects that should be taken into cosideration befor cutting.
|
 VERTICAL CUTS
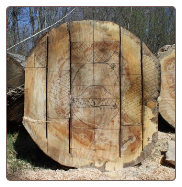 Clean straight cuts pay off later when cutting the blanks on the band-saw and when mounting on the lathe.
|
 SECTIONED
 MARK FOR FINAL CUTS
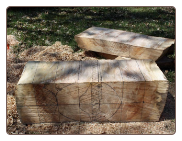 Befor cutting, inspect each face of the slab, note and mark knots and if possible consider the direction the knots pass through the wood and how you can avoid or incorperate the defect into the bowl.
|
 FINAL CUTS
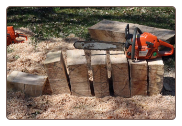 I left the pith on the center block for be turned away on the lathe.
|
 BAND-SAW READY BLOCKS
 BLANKS READY FOR ROUGH TURNING
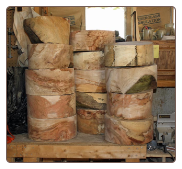 I'll bag these blanks in 33gal plastic trash bags to keep them fresh. Some of the blanks are spalted so if I don't get to them for a couple of weeks (or months as is sometimes the case) I'm not concerned with a little fungus growing.
|
 SELLING YOUR BOWLS
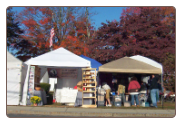 Art festivals are a great way to sell your work.
Get a copy of Sunshine Artist, it lists all the art fairs nation wide with dates, cost, deadlines, and requirments and rates them. Registration deadlins for summer art fairs starts in February and usualy end in April. Fees range from $175 to $350 for a weekend event. In three shows I attended last year I was the only bowl turner in the show. I've found that retuning to the same show for consecutive years should improve your sales volume.
|
 BOWL DISPLAY
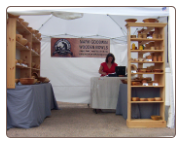 Everything should be at least table hight and ideally no higher than the average woman can reach. My top shelf is too high (I've since cut the shelves down by 6") but, if you're always in the booth you can hand bowls down for your customers. Have a profesional banner made with your name, logo, location, and website if you have one ($100).
|
 David Pye: THE NATURE AND ART OF WORKMANSHIP
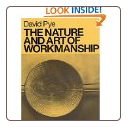 A must-have book for your library! After over 40 years this book is still in print for good reason.
|
|